Over the next decades, downtown Denver’s population will likely double. But that’s not the only place growth is happening. The city’s also sprawling into the sunflower fields of the Eastern Plains, past Peña Boulevard, near Tower Road.
There, new homes are filling the yawning gap between the rest of the city and the airport, in some of the last massive open spaces within Denver’s boundaries.
That kind of sprawl conjures up images of the shoddily built chip-board McMansions of the ’90s on palatial lots. But that isn’t quite right. The lots are smaller than they were back then, fitting in more homes in a compressed space.
The new burbs include a mix of condos and apartments, big multistory houses for larger families, smaller townhomes and stand-alone houses packed onto tiny lots.
Developer Pat Hamill’s Oakwood Homes has a new line, On2 Homes, an experiment in how to create naturally affordable houses.
The motto: “A new type of home. A new way to build.”
Here’s the company’s promise on its website: “On2 Homes is here to disrupt the status quo and construct something stronger that fits us even better.”
But how?
On2 packs together two-story, factory-made, single-family houses in an efficient process that would make Henry Ford proud. Right now, the first few homes in the line have been built in Green Valley Ranch.
These aren’t masterworks of interesting architecture. But they’re also a step up in design from trailers. And while these so-called “modular homes” do have a cookie-cutter feel on the outside, the insides are wide open, beautiful places to live.
Instead of building what the company thinks people want and hoping people come, On2 has been hosting focus groups to learn about what’s working with their first few builds — and what isn’t.
No doubt, the houses are manufactured quickly and treated like mass products — but it’s the customization that makes these homes stand out.
The process for designing them is very sci-fi.
When people consider buying one, they strap on virtual reality goggles to wander a non-existent home, picking rooms and how they would be situated. That same day, buyers can sign a contract. And within a few months, their house will be built.
So far, just one of these homes is occupied, and the idea is still very much in the early phase.
But if the company can strike the balance between affordability and quality and not mass produce acres of one-size-fits-all lemons, Oakwood Homes will cash in on a market that is being underserved by builders: People who work in Denver and don’t have cushy jobs but do want a house of their own. Teachers, sanitation workers, bartenders, accountants, construction workers, grocery clerks and their families would benefit from having equity by owning a house or condo, too.
These On2 homes are designed for first-time home buyers. They sell for half the median house price, which was $620,000 in metro Denver in August. If the company’s predictions are right, people who own these factory-built homes will gain equity just like any other homeowner.
That matters to ON2’s financial director Jordyn Croom.
Croom’s dad’s family lived in Globeville for decades. Their mom’s lived in Montbello. These days, many of their relatives can’t afford Denver.
Displacement is a sad truth for Croom, who spent some of their teenage years effectively homeless and their adult years working their way up in a home-building industry that all too often focuses on building houses, apartments and condos for wealthy people.
“I saw how massively important homeownership is,” Croom said. “It affected my friendships. It affected my physical health, my mental health. This is a very important thing. And we see rent prices right now. They are going through the roof.”
As Croom has made their way through the industry over the past decade, working in nearly every role at Oakwood, they have watched their family get priced out of Denver as rent and home prices skyrocketed. Some aunts and uncles were pushed all the way to the last affordable place they could find: rural Missouri.
When Croom was studying home building at the University of Denver, they imagined spending their adult years sticking it to greedy developers. But soon they decided to work on innovative construction projects that reduced costs for everyday residents. They said it would be more rewarding and effective in addressing the plight of people who want to live here but cannot afford it.
The idea of building homes in factories turns a lot of people off, Croom acknowledged. And the company is working on shifting public perceptions of what so-called “modular housing” is.
A lot of people think factory-made homes sound cheap, unsturdy, and not up to par with hand-built homes, Croom said. But a walk through an On2 Homes property tells a different story.
While the exteriors of all of those homes have a monotonous aesthetic, inside these places are roomy, filled with natural light and comfortable amenities.
And factory builds may actually lead to sturdier homes, Croom said.
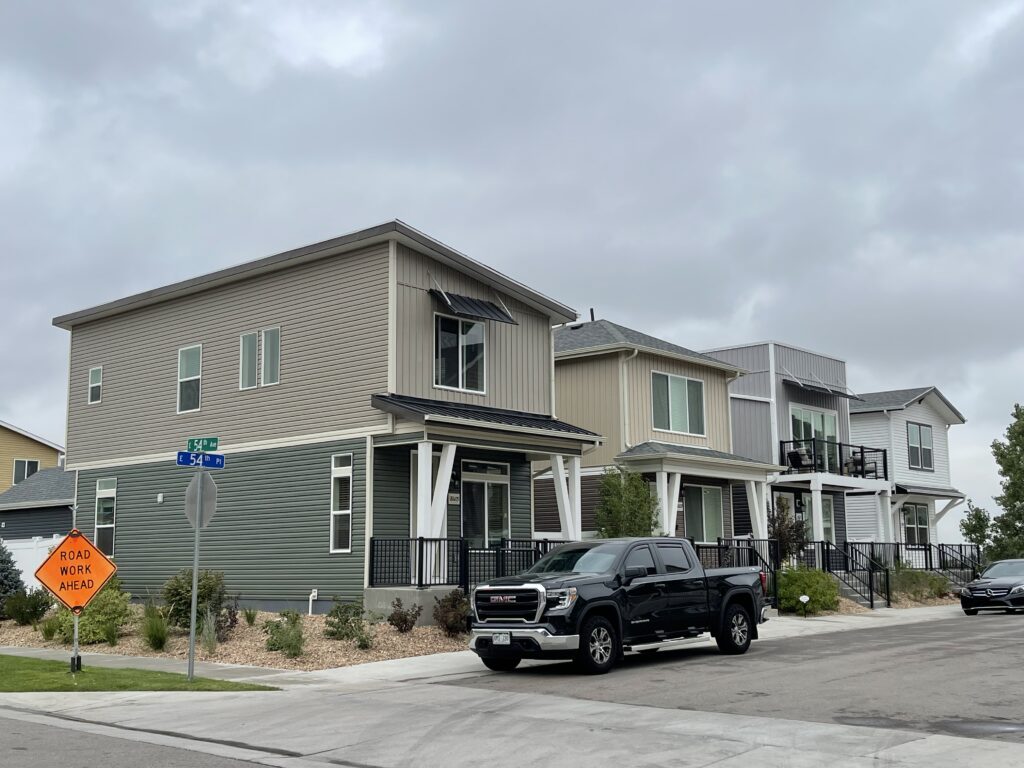
“What is a little bit funny about that is that it technically, academically speaking, would be a superior way of building,” they said. “You’re building it in a factory where it’s always 72 degrees and sunny. You don’t have exposure to the weather elements over a nine-month build time. It’s all precision cut. It’s using the latest and greatest of manufacturing technology to be able to help construct this home. In theory, it’s actually built tighter, better, stronger.”
The team at On2 prides itself on its staff’s diversity, which informs who the company builds for: People who don’t fit the nuclear family mold.
“I think that’s unique in this industry,” Croom said. “On2 is basically female lead. And I’m a non-binary individual. I have a non-traditional family. We had all of that thought process going into it, which I think is a little bit rare in homebuilding today.”
While there is a stigma that needs to be dealt with, Croom believed they will gain equity, like any other house in the area, over time.
Eventually, On2’s modular homes could serve as a national model of how the market can ensure various classes of buyers can own and invest in homes, even in a housing crisis.
Yet the true test of the worth of these properties, their durability and equity will take decades to determine.
On2 has 96 home sites in Green Valley Ranch and is in conversations with politicians at the state and local levels, and other municipalities, about expanding the model statewide.
Eventually, the company hopes to cut the time it takes to build a house.
“We don’t want to deliver anything less than what we consider to be our highest quality,” Croom said. “So in this learning process, it’s a little bit longer. But we have the potential, once we start really getting into the swing of things, of being able to have someone go under contract and 60 days later have a brand new home.”
"Factory" - Google News
September 24, 2022 at 11:00AM
https://ift.tt/PG048Qz
These Green Valley Ranch houses were made in a factory! They're way better (and cheaper) than they sound - Denverite
"Factory" - Google News
https://ift.tt/wIVLud1
Shoes Man Tutorial
Pos News Update
Meme Update
Korean Entertainment News
Japan News Update
Bagikan Berita Ini
0 Response to "These Green Valley Ranch houses were made in a factory! They're way better (and cheaper) than they sound - Denverite"
Post a Comment